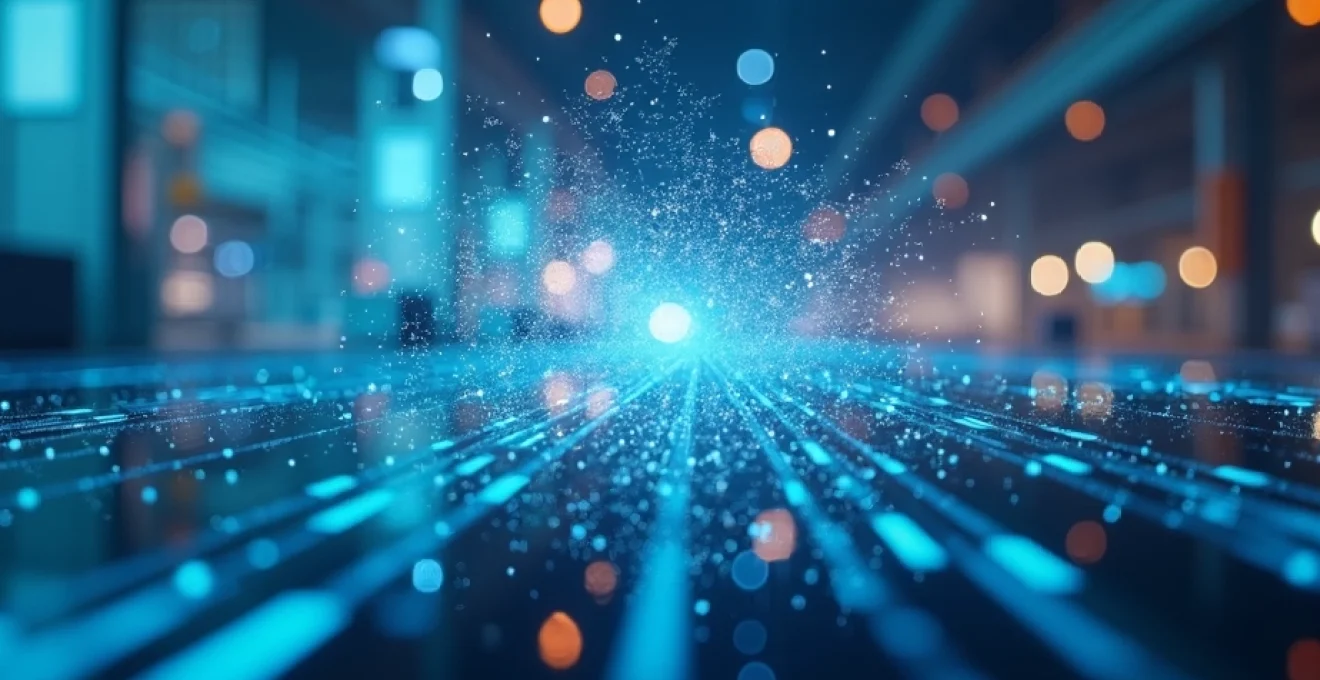
La transformation digitale révolutionne le paysage industriel, redéfinissant les modèles d'affaires et les processus de production. Cette évolution technologique offre aux entreprises industrielles des opportunités sans précédent pour améliorer leur efficacité, leur compétitivité et leur capacité d'innovation. En adoptant les technologies numériques, les industries peuvent optimiser leurs opérations, réduire leurs coûts et répondre plus efficacement aux demandes changeantes du marché. Cependant, cette transition vers l'industrie 4.0 n'est pas sans défis. Les entreprises doivent naviguer dans un écosystème technologique complexe, repenser leurs stratégies et adapter leurs compétences pour tirer pleinement parti de cette révolution numérique.
Enjeux de la transformation digitale dans l'industrie 4.0
La transformation digitale dans le contexte de l'industrie 4.0 représente un changement de paradigme pour les entreprises industrielles. Elle implique l'intégration de technologies avancées dans l'ensemble des processus de production et de gestion, visant à créer des usines intelligentes capables de s'adapter rapidement aux fluctuations du marché et aux exigences des clients.
L'un des principaux enjeux de cette transformation est l'amélioration de la productivité. Les technologies numériques permettent d'exploiter les données numériques pour optimiser les processus de production, réduire les temps d'arrêt et augmenter la qualité des produits. Par exemple, l'analyse des données en temps réel peut aider à identifier et à résoudre les problèmes de production avant qu'ils ne deviennent critiques.
Un autre défi majeur est la personnalisation de masse. Les consommateurs demandent de plus en plus des produits sur mesure, ce qui pousse les industriels à rechercher des solutions pour produire des biens personnalisés à grande échelle, sans compromettre l'efficacité ou la rentabilité. La digitalisation offre les outils nécessaires pour répondre à cette demande, en permettant une flexibilité accrue des lignes de production.
La gestion de la chaîne d'approvisionnement constitue également un enjeu crucial. La transformation digitale permet une visibilité en temps réel sur l'ensemble de la chaîne logistique, facilitant ainsi la prise de décision et l'optimisation des stocks. Cette transparence accrue aide à réduire les coûts et à améliorer la réactivité face aux changements de la demande.
La transformation digitale n'est pas une option, mais une nécessité pour les entreprises industrielles qui souhaitent rester compétitives dans un marché mondial en constante évolution.
Enfin, la durabilité et l'efficacité énergétique sont devenues des préoccupations majeures. Les technologies numériques offrent des solutions pour réduire l'empreinte carbone des industries, optimiser la consommation d'énergie et favoriser une production plus respectueuse de l'environnement. Ces initiatives ne sont pas seulement bénéfiques pour la planète, mais elles peuvent également générer des économies substantielles et améliorer l'image de marque des entreprises.
Technologies clés pour la numérisation des processus industriels
La numérisation des processus industriels repose sur un ensemble de technologies innovantes qui, lorsqu'elles sont intégrées de manière cohérente, transforment radicalement la façon dont les entreprises conçoivent, produisent et distribuent leurs produits. Ces technologies permettent de créer un environnement de production plus intelligent, plus flexible et plus efficace.
L'internet des objets industriels (IIoT) et capteurs connectés
L'Internet des Objets Industriels (IIoT) constitue l'épine dorsale de l'industrie 4.0. Il s'agit d'un réseau de capteurs, d'appareils et de machines interconnectés qui collectent et partagent des données en temps réel. Ces capteurs connectés peuvent être installés sur pratiquement tous les équipements industriels, des machines de production aux systèmes de transport.
L'IIoT permet une surveillance continue des performances des équipements, facilitant ainsi la maintenance prédictive. En analysant les données collectées, les entreprises peuvent anticiper les pannes potentielles et planifier les interventions de maintenance avant qu'une défaillance ne se produise. Cela se traduit par une réduction significative des temps d'arrêt et une augmentation de la productivité.
De plus, les capteurs connectés fournissent des informations précieuses sur l'utilisation des ressources, permettant aux industriels d'optimiser leur consommation d'énergie et de matières premières. Cette optimisation contribue non seulement à réduire les coûts, mais aussi à améliorer l'empreinte environnementale de l'entreprise.
Intelligence artificielle et machine learning pour l'optimisation
L'intelligence artificielle (IA) et le machine learning transforment la manière dont les industries analysent les données et prennent des décisions. Ces technologies permettent de traiter d'énormes volumes de données générées par les capteurs IIoT et d'en extraire des insights précieux pour l'optimisation des processus.
Dans le contexte industriel, l'IA peut être utilisée pour :
- Optimiser les paramètres de production en temps réel
- Prévoir la demande et ajuster la production en conséquence
- Détecter les anomalies et les défauts de qualité avec une précision accrue
- Améliorer la planification de la maintenance prédictive
Le machine learning, en particulier, permet aux systèmes industriels d'apprendre et de s'améliorer continuellement à partir des données collectées. Par exemple, un algorithme de machine learning peut analyser les données historiques de production pour identifier les conditions optimales de fonctionnement des machines, permettant ainsi d'augmenter la qualité des produits tout en réduisant les coûts.
Robotique collaborative et automatisation avancée
La robotique collaborative, ou cobotique , représente une avancée significative dans l'automatisation industrielle. Contrairement aux robots industriels traditionnels, les cobots sont conçus pour travailler aux côtés des humains, combinant la précision et la force des machines avec la flexibilité et l'intelligence des opérateurs humains.
Ces robots collaboratifs offrent plusieurs avantages :
- Une flexibilité accrue dans les processus de production
- Une amélioration de la sécurité des travailleurs
- Une productivité augmentée grâce à la combinaison des compétences humaines et robotiques
- Une facilité d'intégration dans les lignes de production existantes
L'automatisation avancée, quant à elle, s'étend au-delà de la simple robotique pour englober des systèmes complets de production automatisée. Ces systèmes intègrent des technologies telles que la vision par ordinateur, les systèmes de guidage laser et les contrôleurs logiques programmables (PLC) pour créer des lignes de production hautement efficaces et flexibles.
Jumeaux numériques et simulation de production
Les jumeaux numériques représentent une innovation majeure dans la conception et l'optimisation des processus industriels. Un jumeau numérique est une réplique virtuelle d'un produit, d'un processus ou d'un système physique entier. Cette technologie permet aux industriels de simuler, tester et optimiser leurs opérations dans un environnement virtuel avant de les mettre en œuvre dans le monde réel.
Les avantages des jumeaux numériques sont nombreux :
- Réduction des temps et coûts de développement
- Optimisation des performances des produits et des processus
- Anticipation et résolution des problèmes avant qu'ils ne surviennent
- Facilitation de la maintenance prédictive
- Amélioration continue basée sur des données réelles
La simulation de production, étroitement liée aux jumeaux numériques, permet aux entreprises de modéliser et d'analyser leurs processus de fabrication dans un environnement virtuel. Cette approche facilite l'identification des goulots d'étranglement, l'optimisation des flux de travail et la planification de scénarios complexes sans perturber les opérations réelles.
Blockchain pour la traçabilité et la sécurité des données
La blockchain
émerge comme une technologie cruciale pour assurer la traçabilité et la sécurité des données dans l'industrie 4.0. Cette technologie de registre distribué offre un moyen inaltérable et transparent de suivre chaque étape du processus de production, de la source des matières premières jusqu'à la livraison du produit final.
Dans le contexte industriel, la blockchain peut être utilisée pour :
- Garantir l'authenticité et l'origine des produits
- Sécuriser les échanges de données entre partenaires de la chaîne d'approvisionnement
- Automatiser les processus de conformité et d'audit
- Faciliter la gestion des contrats intelligents avec les fournisseurs et les clients
La sécurité des données est un aspect critique de la transformation digitale, et la blockchain offre une solution robuste pour protéger les informations sensibles contre les altérations et les accès non autorisés. Cette technologie joue un rôle essentiel dans l'établissement de la confiance entre les différents acteurs de l'écosystème industriel numérique.
Implémentation de la transformation digitale en entreprise
L'implémentation de la transformation digitale dans une entreprise industrielle est un processus complexe qui nécessite une approche structurée et une vision claire. Cette démarche implique non seulement l'adoption de nouvelles technologies, mais aussi une refonte profonde des processus métiers et de la culture d'entreprise.
Audit digital et feuille de route stratégique
La première étape cruciale de toute transformation digitale est la réalisation d'un audit digital approfondi. Cet audit permet d'évaluer la maturité numérique de l'entreprise, d'identifier les opportunités d'amélioration et de définir les priorités d'action. Il couvre généralement plusieurs aspects tels que les infrastructures IT, les compétences numériques des employés, les processus métiers existants et la culture d'innovation de l'entreprise.
Sur la base des résultats de l'audit, une feuille de route stratégique doit être élaborée. Cette feuille de route définit les objectifs à court, moyen et long terme de la transformation digitale, ainsi que les étapes concrètes pour les atteindre. Elle doit être alignée avec la stratégie globale de l'entreprise et prendre en compte les contraintes budgétaires et opérationnelles.
Un plan de transformation digitale réussi nécessite une vision claire, un leadership fort et un engagement à long terme de toute l'organisation.
Refonte des processus métiers (BPR) pour l'ère numérique
La refonte des processus métiers (Business Process Reengineering ou BPR) est une étape essentielle de la transformation digitale. Il ne s'agit pas simplement de numériser les processus existants, mais de les repenser entièrement pour tirer pleinement parti des nouvelles technologies.
Cette refonte implique souvent :
- L'élimination des tâches redondantes ou à faible valeur ajoutée
- L'automatisation des processus répétitifs
- L'intégration des flux de données entre différents départements
- La mise en place de boucles de rétroaction pour une amélioration continue
- L'adoption de méthodologies agiles pour une plus grande flexibilité
La refonte des processus doit être menée en étroite collaboration avec les équipes opérationnelles, qui apportent leur expertise métier et leur compréhension des défis quotidiens. Cette approche collaborative garantit que les nouveaux processus sont non seulement technologiquement avancés, mais aussi pratiques et adaptés aux réalités du terrain.
Gestion du changement et formation des équipes
La gestion du changement est un aspect critique de la transformation digitale, souvent sous-estimé. L'introduction de nouvelles technologies et de nouveaux modes de travail peut susciter des résistances au sein des équipes. Il est donc essentiel de mettre en place une stratégie de gestion du changement efficace pour accompagner les collaborateurs tout au long de cette transition.
Cette stratégie doit inclure :
- Une communication claire et régulière sur les objectifs et les bénéfices de la transformation
- L'implication des employés dans le processus de changement
- La formation continue pour développer les compétences numériques
- La mise en place de programmes de mentorat et de partage des connaissances
- La reconnaissance et la valorisation des initiatives innovantes
La formation des équipes est un élément clé de cette gestion du changement. Elle doit couvrir non seulement les aspects techniques des nouvelles technologies, mais aussi les nouvelles méthodes de travail et les compétences transversales nécessaires dans un environnement numérique (collaboration à distance, gestion de projet agile, data literacy , etc.).
Intégration des systèmes d'information industriels
L'intégration des systèmes d'information industriels est un défi technique majeur de la transformation digitale. Il s'agit de connecter et de faire communiquer efficacement les différents systèmes utilisés dans l'entreprise, tels que les ERP (Enterprise Resource Planning), les MES (Manufacturing Execution Systems), les SCADA (Supervisory Control and Data Acquisition) et les systèmes de gestion de la qualité.
Cette intégration vise à créer un flux d'information continu et cohérent à travers toute l'entreprise, du niveau opérationnel au niveau stratégique. Elle permet :
- Une visibilité en temps réel sur les opérations
- Une prise de décision plus rapide et mieux informée
- Une optimisation des processus inter-départements
- Une meilleure traçabilité et un contrôle qualité renforcé
L'intégration des
systèmes d'information industriels est un processus complexe qui nécessite une planification minutieuse et une expertise technique approfondie. Il est souvent nécessaire de faire appel à des intégrateurs spécialisés pour mener à bien ces projets d'envergure.
Cas d'usage de la digitalisation dans différents secteurs industriels
Industrie automobile : production personnalisée et maintenance prédictive
L'industrie automobile est à l'avant-garde de la transformation digitale, adoptant des technologies innovantes pour répondre aux demandes croissantes de personnalisation et d'efficacité. La production personnalisée est devenue une réalité grâce à des lignes de production flexibles et à l'utilisation de données clients pour configurer les véhicules selon les préférences individuelles.
La maintenance prédictive, basée sur l'analyse en temps réel des données collectées par des capteurs IoT, permet aux constructeurs automobiles de réduire considérablement les temps d'arrêt et les coûts de maintenance. Par exemple, Volkswagen utilise l'intelligence artificielle pour prédire les pannes de robots dans ses usines, réduisant ainsi les interruptions de production de 36%.
Aéronautique : conception virtuelle et fabrication additive
Dans le secteur aéronautique, la transformation digitale révolutionne les processus de conception et de fabrication. La conception virtuelle, utilisant des outils de CAO avancés et la réalité virtuelle, permet aux ingénieurs de créer et de tester des prototypes numériques avant la production physique. Cela accélère le développement de nouveaux modèles d'avions tout en réduisant les coûts.
La fabrication additive, ou impression 3D, est largement adoptée pour produire des pièces complexes avec une précision accrue et une réduction du gaspillage de matériaux. Airbus, par exemple, utilise l'impression 3D pour produire des pièces d'avion plus légères, contribuant ainsi à réduire la consommation de carburant et les émissions de CO2.
Chimie et pétrochimie : optimisation énergétique et sécurité renforcée
Dans l'industrie chimique et pétrochimique, la digitalisation joue un rôle crucial dans l'optimisation des processus énergétiques et le renforcement de la sécurité. Les technologies d'analyse avancée et l'IoT permettent une gestion plus précise de la consommation d'énergie, réduisant ainsi les coûts opérationnels et l'impact environnemental.
La sécurité, une préoccupation majeure dans ce secteur, bénéficie grandement des technologies numériques. Des systèmes de surveillance en temps réel, couplés à des algorithmes d'intelligence artificielle, peuvent détecter les anomalies et prévenir les incidents avant qu'ils ne se produisent. Par exemple, la société BASF utilise des drones équipés de caméras thermiques pour inspecter ses installations, améliorant ainsi la sécurité tout en réduisant les coûts d'inspection.
Agroalimentaire : traçabilité totale et contrôle qualité automatisé
Le secteur agroalimentaire adopte la transformation digitale pour répondre aux exigences croissantes de traçabilité et de qualité des consommateurs. La blockchain est de plus en plus utilisée pour assurer une traçabilité totale des produits, de la ferme à l'assiette. Cette technologie permet de suivre chaque étape de la chaîne d'approvisionnement, garantissant l'authenticité et la sécurité des aliments.
Le contrôle qualité automatisé, utilisant des systèmes de vision par ordinateur et d'analyse d'images, permet une inspection plus rapide et plus précise des produits. Ces technologies peuvent détecter des défauts invisibles à l'œil nu, assurant ainsi une qualité constante des produits. Nestlé, par exemple, utilise l'intelligence artificielle pour analyser les images des grains de café et optimiser la qualité de ses produits.
Défis et risques de la transformation numérique industrielle
Cybersécurité des systèmes industriels connectés
Avec l'interconnexion croissante des systèmes industriels, la cybersécurité devient un enjeu majeur. Les usines connectées sont des cibles potentielles pour les cyberattaques, qui peuvent avoir des conséquences désastreuses sur la production et la sécurité. Comment les entreprises peuvent-elles protéger leurs infrastructures critiques tout en bénéficiant des avantages de la connectivité ?
La mise en place d'une stratégie de cybersécurité robuste est essentielle. Cela implique non seulement l'utilisation de technologies de sécurité avancées, mais aussi la formation continue des employés aux bonnes pratiques de sécurité. Les entreprises doivent adopter une approche de "sécurité by design", intégrant la sécurité dès la conception des systèmes et des processus.
Interopérabilité des nouvelles technologies avec l'existant
L'un des défis majeurs de la transformation digitale est l'intégration des nouvelles technologies avec les systèmes existants, souvent plus anciens. Cette intégration est comparable à la construction d'un pont entre deux îles : il faut s'assurer que les deux extrémités sont compatibles et stables. Comment les entreprises peuvent-elles moderniser leurs infrastructures tout en préservant la continuité opérationnelle ?
La solution réside souvent dans une approche progressive, utilisant des technologies de middleware et des API pour faciliter la communication entre les anciens et les nouveaux systèmes. Il est également crucial de procéder à une cartographie détaillée des systèmes existants et de planifier soigneusement les phases de migration pour minimiser les perturbations.
Protection des données et conformité réglementaire (RGPD, NIS2)
La transformation digitale s'accompagne d'une explosion du volume de données collectées et traitées, soulevant des questions cruciales de protection et de conformité réglementaire. Le Règlement Général sur la Protection des Données (RGPD) en Europe et la directive NIS2 sur la cybersécurité imposent des obligations strictes aux entreprises en matière de gestion des données.
Pour relever ce défi, les entreprises doivent mettre en place des politiques de gouvernance des données robustes, incluant des processus de collecte, de stockage et de traitement conformes aux réglementations. La nomination d'un Délégué à la Protection des Données (DPO) et la réalisation régulière d'audits de conformité sont des pratiques essentielles pour assurer le respect des normes en vigueur.
Perspectives d'avenir et tendances émergentes
Edge computing et 5G industrielle
L'edge computing et la 5G industrielle s'annoncent comme des technologies transformatives pour l'industrie 4.0. L'edge computing, en traitant les données au plus près de leur source, permet une réduction significative de la latence et une amélioration de la réactivité des systèmes industriels. Combiné à la 5G industrielle, il ouvre la voie à des applications en temps réel ultra-performantes.
Ces technologies vont notamment permettre le développement de véhicules autonomes dans les usines, une automatisation plus poussée des lignes de production, et une maintenance prédictive encore plus précise. Par exemple, Bosch Rexroth utilise déjà l'edge computing et la 5G pour optimiser ses processus de fabrication, réduisant ainsi les temps d'arrêt et améliorant la flexibilité de production.
Réalité augmentée pour la maintenance et la formation
La réalité augmentée (RA) émerge comme un outil puissant pour la maintenance industrielle et la formation des opérateurs. En superposant des informations numériques au monde réel, la RA permet aux techniciens de maintenance d'accéder à des instructions détaillées et des visualisations en temps réel, améliorant ainsi l'efficacité et la précision des interventions.
Dans le domaine de la formation, la RA offre des possibilités immersives pour simuler des situations réelles sans risque. Siemens, par exemple, utilise la réalité augmentée pour former ses employés à l'utilisation de machines complexes, réduisant ainsi le temps de formation et améliorant la rétention des connaissances.
Économie circulaire et industrie durable par le numérique
La transformation digitale joue un rôle crucial dans la transition vers une économie circulaire et une industrie plus durable. Les technologies numériques permettent une meilleure traçabilité des matériaux, facilitant ainsi leur réutilisation et leur recyclage. L'analyse de données avancée aide les entreprises à optimiser leur consommation de ressources et à réduire leurs déchets.
Des initiatives comme le "passeport numérique des produits", proposé par l'Union Européenne, illustrent cette tendance. Ce passeport contiendrait des informations sur la composition, la réparabilité et le recyclage des produits, favorisant ainsi une économie plus circulaire. Des entreprises comme Philips adoptent déjà des modèles d'économie circulaire, utilisant la digitalisation pour concevoir des produits plus durables et faciliter leur reconditionnement.
L'avenir de l'industrie réside dans sa capacité à conjuguer performance économique et responsabilité environnementale. La transformation digitale est la clé pour atteindre cet équilibre.