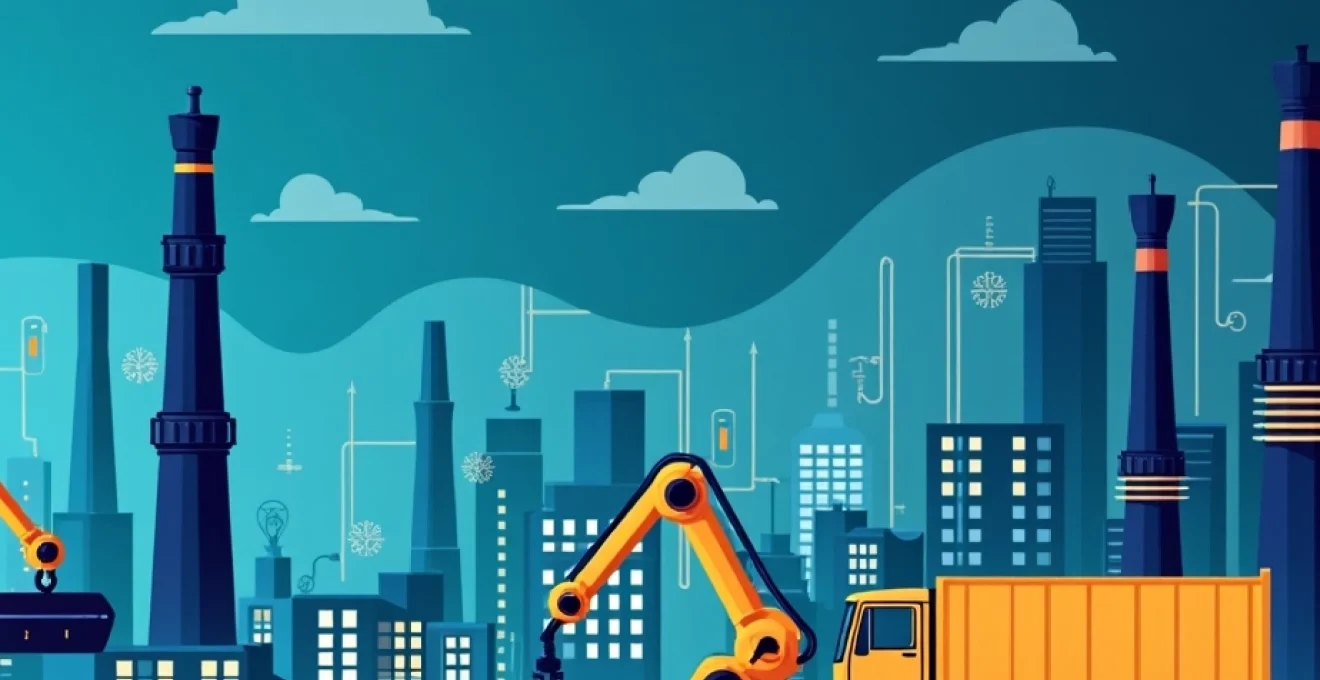
Le secteur industriel connaît une révolution technologique sans précédent, redéfinissant les processus de production et la manière dont les entreprises opèrent. Cette transformation profonde, souvent appelée Industrie 4.0, combine l'automatisation avancée, l'intelligence artificielle et l'Internet des objets pour créer des usines intelligentes et des chaînes d'approvisionnement interconnectées. Les implications de ces changements sont vastes, allant de l'amélioration de l'efficacité opérationnelle à la création de nouveaux modèles économiques. Comment ces innovations façonnent-elles l'avenir de l'industrie ? Quels défis et opportunités présentent-elles pour les entreprises et les travailleurs ?
Évolution technologique du secteur industriel
L'évolution technologique du secteur industriel est marquée par une convergence de technologies avancées qui transforment radicalement les processus de fabrication. Cette mutation ne se limite pas à l'introduction de nouvelles machines ; elle englobe une refonte complète de la manière dont les usines fonctionnent et interagissent avec leur environnement. Les systèmes cyber-physiques , qui intègrent des capacités de calcul, de communication et de contrôle directement dans les équipements physiques, sont au cœur de cette révolution.
L'un des aspects les plus visibles de cette évolution est l'adoption croissante de la fabrication additive , communément appelée impression 3D. Cette technologie permet de créer des objets complexes couche par couche, offrant une flexibilité de conception sans précédent et réduisant considérablement les délais de prototypage. Dans certains secteurs, comme l'aérospatiale, la fabrication additive est déjà utilisée pour produire des composants critiques, démontrant ainsi sa maturité et son potentiel transformateur.
Parallèlement, l'intégration de capteurs intelligents dans pratiquement tous les aspects de la production industrielle génère un flux constant de données en temps réel. Ces informations, traitées par des algorithmes d'analyse avancés, permettent une optimisation continue des processus, une maintenance prédictive et une gestion plus efficace des ressources. Cette approche basée sur les données est en train de redéfinir la notion même d'efficacité industrielle.
Automatisation et robotique dans les chaînes de production
L'automatisation et la robotique sont devenues des éléments incontournables des chaînes de production modernes. Elles offrent une précision, une vitesse et une constance que les opérations manuelles ne peuvent égaler. Les robots industriels, autrefois cantonnés à des tâches répétitives et isolées des travailleurs humains, évoluent vers des systèmes plus flexibles et collaboratifs.
Cobots collaboratifs : l'exemple des robots kuka et universal robots
Les cobots , ou robots collaboratifs, représentent une avancée significative dans l'interaction homme-machine au sein des usines. Contrairement aux robots industriels traditionnels, les cobots sont conçus pour travailler aux côtés des humains en toute sécurité. Des entreprises comme Kuka et Universal Robots sont à l'avant-garde de cette technologie, proposant des solutions qui allient la force et la précision des machines à la flexibilité et à l'intelligence des opérateurs humains.
Par exemple, les cobots de Universal Robots peuvent être facilement programmés pour effectuer une variété de tâches, de l'assemblage précis de petites pièces à la manipulation de matériaux lourds. Leur capacité à s'adapter rapidement à différentes configurations de production les rend particulièrement précieux dans les environnements de fabrication flexibles où les lots de production changent fréquemment.
Systèmes de vision industrielle et contrôle qualité automatisé
Les systèmes de vision industrielle révolutionnent le contrôle qualité en permettant une inspection à 100% des produits à des vitesses impossibles à atteindre manuellement. Ces systèmes utilisent des caméras haute résolution et des algorithmes de traitement d'image sophistiqués pour détecter les défauts les plus infimes, garantissant ainsi une qualité constante et réduisant les taux de rejet.
Dans l'industrie automobile, par exemple, ces systèmes sont utilisés pour inspecter la peinture des carrosseries, détectant des imperfections invisibles à l'œil nu. Cette technologie ne se contente pas de signaler les problèmes ; elle peut également fournir des données précieuses pour améliorer les processus en amont, contribuant ainsi à une amélioration continue de la qualité.
Intelligence artificielle et maintenance prédictive
L'intelligence artificielle (IA) transforme la maintenance industrielle en passant d'une approche réactive ou préventive à une approche prédictive. En analysant les données collectées par des capteurs sur les équipements, les algorithmes d'IA peuvent prédire les pannes avant qu'elles ne se produisent, permettant ainsi une planification optimale des interventions de maintenance.
Cette approche réduit considérablement les temps d'arrêt non planifiés, qui peuvent coûter des millions d'euros par heure dans certaines industries. De plus, elle prolonge la durée de vie des équipements en permettant des interventions ciblées au moment opportun, plutôt que des remplacements systématiques qui peuvent être prématurés ou tardifs.
Véhicules à guidage automatique (AGV) dans la logistique interne
Les véhicules à guidage automatique (AGV) révolutionnent la logistique interne des usines en automatisant le transport de matériaux et de produits finis. Ces robots mobiles peuvent naviguer de manière autonome dans l'environnement de production, évitant les obstacles et optimisant leurs trajets en temps réel.
L'utilisation d'AGV améliore non seulement l'efficacité des opérations logistiques mais contribue également à la sécurité en réduisant le trafic de chariots élévateurs conduits manuellement. De plus, ces systèmes s'intègrent parfaitement dans le concept d'usine intelligente, communiquant avec les systèmes de gestion de la production pour s'adapter dynamiquement aux besoins changeants de la chaîne de production.
Transformation numérique et industrie 4.0
La transformation numérique du secteur industriel, souvent désignée sous le terme d'Industrie 4.0, représente un changement de paradigme dans la manière dont les usines sont conçues et opérées. Cette révolution industrielle se caractérise par l'intégration profonde des technologies numériques dans tous les aspects de la production, créant des systèmes interconnectés et intelligents capables d'optimiser en temps réel l'ensemble de la chaîne de valeur.
Internet des objets industriel (IIoT) et capteurs connectés
L'Internet des objets industriel (IIoT) constitue l'épine dorsale de l'Industrie 4.0. Il s'agit d'un réseau de capteurs, d'actionneurs et de dispositifs intelligents qui collectent et partagent des données en temps réel sur l'ensemble du processus de production. Ces capteurs peuvent surveiller une multitude de paramètres, de la température et de la pression à la vibration et à la consommation d'énergie.
L'impact de l'IIoT sur l'efficacité opérationnelle est considérable. Par exemple, dans une usine de production d'acier, des capteurs connectés peuvent surveiller en permanence la qualité du métal en fusion, ajustant automatiquement les paramètres du processus pour maintenir une qualité optimale tout en minimisant la consommation d'énergie. Cette capacité d'optimisation en temps réel peut se traduire par des économies significatives et une amélioration de la qualité du produit final.
Jumeaux numériques et simulation de processus industriels
Les jumeaux numériques représentent une avancée majeure dans la modélisation et la simulation des processus industriels. Un jumeau numérique est une réplique virtuelle exacte d'un produit, d'un processus ou d'un système physique entier. Cette technologie permet aux ingénieurs de simuler et d'optimiser les opérations dans un environnement virtuel avant de les mettre en œuvre dans le monde réel.
L'utilisation de jumeaux numériques offre de nombreux avantages. Elle permet de tester des scénarios complexes sans risquer d'interrompre la production réelle, d'optimiser les processus de manière itérative, et même de prédire les résultats de changements dans la configuration de production. Dans l'industrie aérospatiale, par exemple, les jumeaux numériques sont utilisés pour simuler le comportement des moteurs d'avion dans diverses conditions, permettant ainsi d'améliorer leur conception et leur maintenance.
Big data et analytique avancée pour l'optimisation de la production
Le Big Data et l'analytique avancée transforment la manière dont les décisions sont prises dans l'environnement industriel. En collectant et en analysant d'énormes volumes de données provenant de multiples sources au sein de l'usine, les entreprises peuvent obtenir des insights précieux pour optimiser leurs opérations.
Ces techniques analytiques avancées peuvent être utilisées pour prédire la demande des clients avec une grande précision, optimiser la planification de la production, réduire les temps d'arrêt des machines et même personnaliser les produits à grande échelle. Par exemple, une entreprise de production de biens de consommation peut utiliser l'analyse prédictive pour ajuster sa production en fonction des tendances du marché, réduisant ainsi les stocks excédentaires et améliorant la réactivité aux changements de la demande.
Cloud computing et edge computing dans l'environnement industriel
Le cloud computing et l'edge computing jouent des rôles complémentaires cruciaux dans l'infrastructure informatique moderne des environnements industriels. Le cloud offre une capacité de stockage et de traitement pratiquement illimitée, permettant l'analyse de grandes quantités de données historiques et la mise en œuvre de modèles d'apprentissage automatique complexes.
L'edge computing, quant à lui, traite les données au plus près de leur source, directement sur les dispositifs ou les passerelles locales. Cette approche est particulièrement utile pour les applications nécessitant une réponse en temps réel, comme le contrôle de qualité en ligne ou la sécurité des machines. En combinant cloud et edge computing, les entreprises peuvent bénéficier à la fois de la puissance de calcul centralisée et de la réactivité locale, créant ainsi des systèmes de production plus intelligents et plus résilients.
Fabrication additive et nouveaux matériaux
La fabrication additive, communément appelée impression 3D, révolutionne les processus de production traditionnels en permettant la création d'objets complexes couche par couche. Cette technologie offre une flexibilité sans précédent dans la conception et la production, ouvrant la voie à de nouvelles possibilités en termes de personnalisation et d'optimisation des produits.
Impression 3D métallique : technologies SLM et EBM
L'impression 3D métallique, en particulier les technologies de fusion sélective par laser (SLM) et de fusion par faisceau d'électrons (EBM), transforme la production de pièces métalliques complexes. Ces technologies permettent de créer des structures légères mais robustes, impossibles à réaliser avec les méthodes de fabrication traditionnelles.
Par exemple, dans l'industrie aérospatiale, l'impression 3D métallique est utilisée pour produire des composants de moteurs d'avion avec des géométries optimisées pour réduire le poids tout en maintenant ou même en améliorant les performances. Cette capacité à produire des pièces "bio-inspirées" avec des structures internes complexes ouvre de nouvelles possibilités en termes d'efficacité énergétique et de réduction des coûts de production.
Matériaux composites avancés dans l'aérospatiale et l'automobile
Les matériaux composites avancés, combinant différents matériaux pour obtenir des propriétés supérieures, jouent un rôle croissant dans les industries aérospatiale et automobile. Ces matériaux offrent un rapport résistance/poids exceptionnellement élevé, ce qui les rend idéaux pour les applications où la légèreté est cruciale.
Dans l'industrie automobile, l'utilisation de composites à base de fibres de carbone permet de réduire significativement le poids des véhicules, améliorant ainsi leur efficacité énergétique sans compromettre la sécurité. De même, dans l'aérospatiale, les composites avancés sont utilisés pour fabriquer des fuselages d'avions plus légers et plus résistants, contribuant à réduire la consommation de carburant et les émissions.
Nanomatériaux et leurs applications industrielles
Les nanomatériaux, avec leurs propriétés uniques à l'échelle nanométrique, ouvrent de nouvelles perspectives dans de nombreux domaines industriels. Ces matériaux peuvent offrir des caractéristiques extraordinaires en termes de résistance, de conductivité ou de réactivité chimique, tout en étant extrêmement légers.
Dans l'industrie électronique, par exemple, les nanotubes de carbone sont explorés pour créer des circuits plus petits et plus efficaces énergétiquement. Dans le secteur de l'énergie, les nanomatériaux sont utilisés pour développer des batteries à haute capacité et des cellules solaires plus efficaces. L'industrie textile bénéficie également de ces avancées, avec des tissus auto-nettoyants ou résistants aux taches grâce à des revêtements nanostructurés.
Efficacité énergétique et durabilité industrielle
L'efficacité énergétique et la durabilité sont devenues des priorités majeures pour le secteur industriel, non seulement pour des raisons environnementales mais aussi économiques. Les entreprises cherchent activement des moyens de réduire leur consommation d'énergie et leur impact environnemental tout en améliorant leur compétitivité.
Systèmes de récupération de chaleur et cogénération
Les systèmes de récupération de chaleur et de cogénération représentent une approche ingénieuse pour améliorer l'efficacité énergétique industrielle. Ces technologies permettent de capturer et de réutiliser la chaleur qui serait autrement perdue dans les processus industriels, transformant ce qui était considéré comme un déchet en une ressource précieuse.
Par exemple, dans une usine sidérurgique, la chaleur résiduelle des fours peut être récupérée pour générer de l'électricité ou pour chauffer d'
autres processus industriels. Les systèmes de cogénération vont encore plus loin en produisant simultanément de l'électricité et de la chaleur à partir d'une seule source d'énergie, maximisant ainsi l'efficacité globale du système.
Dans l'industrie agroalimentaire, par exemple, la vapeur générée par les chaudières peut être utilisée non seulement pour le chauffage mais aussi pour produire de l'électricité via des turbines à vapeur. Cette approche peut réduire considérablement la dépendance aux sources d'énergie externes et diminuer l'empreinte carbone de l'entreprise.
Intégration des énergies renouvelables dans les processus industriels
L'intégration des énergies renouvelables dans les processus industriels représente une étape cruciale vers la durabilité du secteur. De plus en plus d'entreprises investissent dans des installations solaires, éoliennes ou de biomasse pour réduire leur dépendance aux combustibles fossiles et minimiser leur impact environnemental.
Par exemple, certaines usines de production automobile ont installé des panneaux solaires sur leurs toits, générant une partie significative de l'électricité nécessaire à leurs opérations. D'autres industries, comme la production de papier, utilisent les déchets de bois comme biomasse pour alimenter leurs chaudières, créant ainsi un cycle de production presque fermé en termes d'énergie.
Économie circulaire et gestion des déchets industriels
L'économie circulaire est un concept qui gagne du terrain dans le secteur industriel, visant à minimiser les déchets et à maximiser la réutilisation des ressources. Cette approche implique de repenser les processus de production pour créer des boucles fermées où les déchets d'un processus deviennent les matières premières d'un autre.
Dans l'industrie chimique, par exemple, les sous-produits d'une réaction peuvent être récupérés et utilisés comme intrants pour d'autres processus, réduisant ainsi les déchets et la consommation de matières premières. De même, dans l'industrie métallurgique, les scories, autrefois considérées comme des déchets, sont maintenant valorisées dans la production de ciment ou la construction routière.
Sécurité et cybersécurité industrielle
Avec la numérisation croissante des processus industriels, la sécurité et la cybersécurité sont devenues des préoccupations majeures pour les entreprises. Les systèmes interconnectés et les données en temps réel offrent de nombreux avantages, mais ils créent également de nouvelles vulnérabilités qui doivent être soigneusement gérées.
Systèmes de contrôle industriels (ICS) et protection SCADA
Les systèmes de contrôle industriels (ICS) et les systèmes SCADA (Supervisory Control and Data Acquisition) sont au cœur des opérations industrielles modernes. Ils permettent de surveiller et de contrôler les processus industriels à distance, offrant une efficacité et une flexibilité accrues. Cependant, leur connectivité les rend également vulnérables aux cyberattaques.
La protection de ces systèmes implique une approche multicouche, combinant des pare-feux, des systèmes de détection d'intrusion, et des protocoles de communication sécurisés. De plus, la ségrégation des réseaux et l'implémentation de principes de moindre privilège sont essentielles pour limiter l'impact potentiel d'une brèche de sécurité.
Normes ISO/IEC 62443 pour la sécurité des systèmes d'automatisation
Les normes ISO/IEC 62443 fournissent un cadre complet pour la sécurité des systèmes d'automatisation et de contrôle industriels. Ces normes couvrent tous les aspects de la sécurité, de la gestion des risques à la mise en œuvre technique, en passant par les processus organisationnels.
L'adoption de ces normes permet aux entreprises de mettre en place une approche systématique de la cybersécurité, adaptée aux spécificités de l'environnement industriel. Elles prennent en compte non seulement la protection contre les menaces externes, mais aussi la gestion des accès internes et la sécurité tout au long du cycle de vie des systèmes.
Détection et prévention des intrusions dans les réseaux industriels
La détection et la prévention des intrusions dans les réseaux industriels nécessitent des outils et des approches spécifiques, adaptés aux protocoles et aux contraintes de l'environnement industriel. Contrairement aux réseaux informatiques traditionnels, les réseaux industriels ont souvent des exigences strictes en termes de latence et de disponibilité.
Les solutions de détection d'intrusion pour l'industrie utilisent des techniques d'analyse comportementale pour identifier les anomalies dans les flux de données industrielles. Ces systèmes peuvent détecter non seulement les tentatives d'intrusion malveillantes, mais aussi les dysfonctionnements potentiels des équipements, offrant ainsi une double fonction de sécurité et de maintenance prédictive.