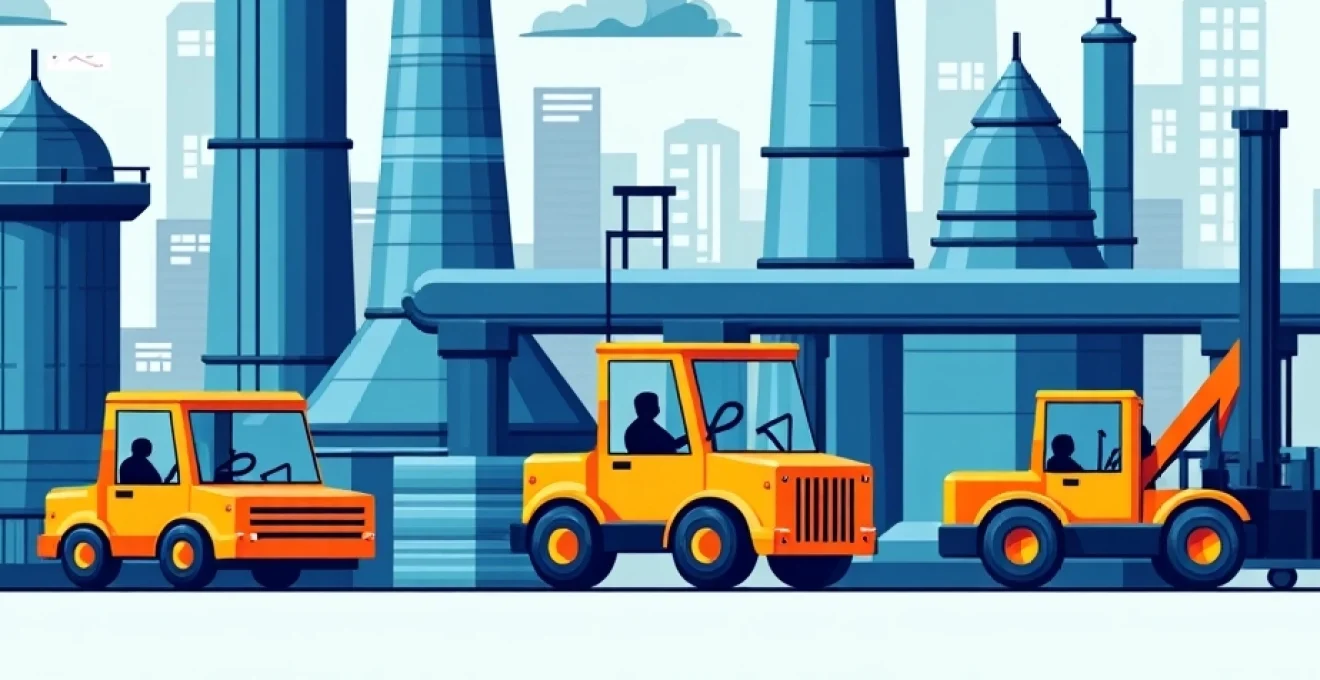
Le secteur industriel connaît une transformation profonde à l'ère du numérique et de l'innovation technologique. Les entreprises industrielles font face à des défis majeurs pour rester compétitives dans un environnement en constante évolution. De l'optimisation des processus de fabrication à la gestion de la chaîne d'approvisionnement, en passant par l'innovation et la durabilité, ces organisations doivent s'adapter rapidement pour tirer parti des nouvelles opportunités. Cet article explore les tendances clés et les enjeux auxquels sont confrontées les entreprises industrielles modernes, offrant un aperçu des stratégies et technologies qui façonnent l'avenir de l'industrie.
Évolution des processus de fabrication dans l'industrie 4.0
L'industrie 4.0, aussi appelée quatrième révolution industrielle, transforme radicalement les processus de fabrication traditionnels. Cette nouvelle ère industrielle se caractérise par l'intégration de technologies avancées telles que l' intelligence artificielle , l' Internet des objets (IoT), et les systèmes cyber-physiques . Ces innovations permettent une production plus flexible, efficace et personnalisée.
L'un des aspects les plus marquants de l'industrie 4.0 est l'automatisation poussée des lignes de production. Les robots collaboratifs, ou cobots
, travaillent aux côtés des humains, augmentant la productivité tout en améliorant la sécurité. Les systèmes de fabrication additive, comme l'impression 3D, révolutionnent la production de pièces complexes et permettent une personnalisation de masse à moindre coût.
La collecte et l'analyse de données en temps réel jouent également un rôle crucial dans l'optimisation des processus. Les capteurs intégrés aux machines collectent en permanence des informations sur leur performance, permettant une maintenance prédictive et une réduction des temps d'arrêt. Cette approche data-driven améliore considérablement l'efficacité opérationnelle des usines.
L'industrie 4.0 n'est pas seulement une évolution technologique, c'est une révolution dans la manière de concevoir, produire et livrer les produits.
Les entreprises industrielles qui adoptent ces technologies constatent souvent une amélioration significative de leur productivité, de leur qualité et de leur flexibilité. Cependant, cette transition nécessite des investissements importants et une refonte des compétences de la main-d'œuvre. La formation continue et l'adaptation des employés aux nouvelles technologies deviennent donc des enjeux stratégiques pour les industriels.
Gestion de la chaîne d'approvisionnement et logistique industrielle
La gestion efficace de la chaîne d'approvisionnement est devenue un élément crucial de la compétitivité des entreprises industrielles. Dans un contexte de mondialisation et de demande croissante pour des livraisons rapides et personnalisées, les industriels doivent optimiser chaque maillon de leur chaîne logistique.
Optimisation des flux avec le système MRP II
Le système MRP II
(Manufacturing Resource Planning) est un outil puissant pour la planification et le contrôle de la production. Il intègre la gestion des commandes, la planification de la production, la gestion des stocks et la comptabilité. En utilisant le MRP II, les entreprises peuvent mieux synchroniser leurs ressources et réduire les coûts liés aux excédents de stock ou aux ruptures d'approvisionnement.
L'implémentation réussie d'un système MRP II requiert une analyse approfondie des processus de l'entreprise et une formation adéquate du personnel. Les bénéfices incluent une meilleure visibilité sur l'ensemble de la chaîne de production et une capacité accrue à répondre rapidement aux fluctuations de la demande.
Intégration des technologies RFID pour le suivi des stocks
La technologie RFID (Radio Frequency Identification) révolutionne la gestion des stocks dans l'industrie. En attachant des étiquettes RFID aux produits et aux composants, les entreprises peuvent suivre en temps réel le mouvement des marchandises tout au long de la chaîne d'approvisionnement. Cette visibilité accrue permet d'optimiser les niveaux de stock, de réduire les pertes et d'améliorer la traçabilité des produits.
L'intégration de la RFID avec les systèmes de gestion d'entrepôt (WMS) offre des avantages supplémentaires, comme l'automatisation des processus de réception et d'expédition. Cependant, le déploiement de cette technologie nécessite un investissement initial important et une réflexion sur la gestion des données collectées.
Stratégies de lean manufacturing et kanban
Le lean manufacturing vise à éliminer les gaspillages et à maximiser la valeur ajoutée à chaque étape de la production. Le système Kanban, un élément clé du lean, utilise des signaux visuels pour déclencher la production ou le réapprovisionnement des stocks uniquement lorsque c'est nécessaire. Cette approche pull permet de réduire les stocks intermédiaires et d'améliorer la fluidité de la production.
La mise en place d'une stratégie lean nécessite un changement culturel au sein de l'entreprise. Elle implique une responsabilisation des employés et une recherche constante d'amélioration continue. Les entreprises qui réussissent à implémenter ces principes constatent souvent une réduction significative des coûts et une amélioration de la qualité.
Gestion des fournisseurs et approvisionnement stratégique
La gestion efficace des relations avec les fournisseurs est cruciale pour assurer la stabilité et la performance de la chaîne d'approvisionnement. L'approvisionnement stratégique va au-delà de la simple recherche du meilleur prix; il prend en compte des facteurs tels que la qualité, la fiabilité et la capacité d'innovation des fournisseurs.
Les entreprises industrielles modernes développent des partenariats à long terme avec leurs fournisseurs clés, impliquant parfois ces derniers dès la phase de conception des produits. Cette collaboration étroite permet d'optimiser les coûts, d'améliorer la qualité et de réduire les délais de mise sur le marché des nouveaux produits.
Une chaîne d'approvisionnement agile et résiliente est un avantage concurrentiel majeur dans l'industrie moderne.
Innovation et R&D dans le secteur industriel
L'innovation est le moteur de la croissance et de la compétitivité dans le secteur industriel. Les entreprises qui investissent massivement dans la recherche et le développement (R&D) sont mieux positionnées pour anticiper les besoins du marché et développer des produits à forte valeur ajoutée.
Développement de nouveaux matériaux composites
Les matériaux composites, combinant les propriétés de différents matériaux, ouvrent de nouvelles perspectives dans de nombreux secteurs industriels. Ces matériaux offrent souvent un excellent rapport résistance/poids, des propriétés thermiques améliorées ou une meilleure résistance à la corrosion. Le développement de nouveaux composites, notamment à base de fibres de carbone ou de nanoparticules, permet de créer des produits plus légers, plus résistants et plus durables.
L'industrie aérospatiale est particulièrement à la pointe dans l'utilisation de ces matériaux innovants, cherchant constamment à réduire le poids des aéronefs pour améliorer leur efficacité énergétique. Les défis liés au développement de ces matériaux incluent la maîtrise des processus de fabrication complexes et la gestion du cycle de vie, notamment le recyclage en fin de vie.
Applications de l'intelligence artificielle dans la conception industrielle
L'intelligence artificielle (IA) transforme radicalement les processus de conception industrielle. Les algorithmes d'apprentissage automatique peuvent analyser d'énormes quantités de données pour optimiser la conception des produits, prédire les performances et simuler différents scénarios d'utilisation. Cette approche, connue sous le nom de generative design
, permet d'explorer rapidement un grand nombre d'alternatives de conception et de trouver des solutions innovantes que les ingénieurs n'auraient peut-être pas envisagées.
L'IA est également utilisée pour améliorer la qualité et la fiabilité des produits. En analysant les données de performance et de défaillance, elle peut identifier les points faibles potentiels et suggérer des améliorations. Cette approche prédictive permet de réduire les coûts de développement et d'accélérer la mise sur le marché de nouveaux produits.
Ingénierie simultanée et prototypage rapide
L'ingénierie simultanée, aussi appelée concurrent engineering , est une approche qui vise à réduire le temps de développement des produits en parallélisant les différentes phases de conception et de production. Cette méthodologie s'appuie sur des outils de collaboration avancés qui permettent aux équipes de travailler simultanément sur différents aspects du projet.
Le prototypage rapide, facilité par les technologies d'impression 3D, joue un rôle crucial dans cette approche. Il permet de créer rapidement des modèles physiques pour tester et valider les concepts, réduisant ainsi les cycles de développement et les coûts associés. Cette itération rapide entre la conception et le prototypage accélère l'innovation et permet une meilleure adaptation aux besoins du marché.
Collaboration industrie-université pour l'innovation ouverte
La collaboration entre les entreprises industrielles et les institutions académiques est devenue un pilier de l'innovation ouverte. Ces partenariats permettent aux industriels d'accéder à des connaissances de pointe et à des talents prometteurs, tandis que les universités bénéficient de financements et d'une exposition aux défis concrets de l'industrie.
De nombreuses entreprises établissent des laboratoires conjoints avec des universités ou participent à des consortiums de recherche. Ces collaborations se concentrent souvent sur des domaines émergents tels que la nanotechnologie, les matériaux avancés ou l'intelligence artificielle appliquée à l'industrie. Le succès de ces partenariats repose sur une définition claire des objectifs, une gestion efficace de la propriété intellectuelle et une communication ouverte entre les parties prenantes.
Transformation numérique et industrie connectée
La transformation numérique est au cœur de l'évolution des entreprises industrielles modernes. Elle implique l'intégration de technologies digitales avancées dans tous les aspects de l'activité, de la production à la relation client, en passant par la gestion des opérations. Cette mutation profonde permet aux industriels de gagner en efficacité, de réduire les coûts et d'offrir de nouveaux services à valeur ajoutée.
Implémentation de jumeaux numériques dans la production
Le concept de jumeau numérique révolutionne la manière dont les entreprises conçoivent, produisent et maintiennent leurs produits et systèmes. Un jumeau numérique est une réplique virtuelle d'un objet ou d'un processus physique, alimentée en temps réel par des données provenant de capteurs. Cette technologie permet de simuler, prédire et optimiser les performances des systèmes industriels avec une précision sans précédent.
Dans le contexte de la production, les jumeaux numériques offrent de nombreux avantages. Ils permettent de tester virtuellement des modifications de la ligne de production avant leur mise en œuvre physique, réduisant ainsi les risques et les coûts associés aux changements. De plus, en analysant les données en temps réel, ils facilitent la détection précoce des anomalies et l'optimisation continue des processus.
Utilisation de l'IoT industriel pour la maintenance prédictive
L'Internet des Objets industriel (IIoT) transforme radicalement l'approche de la maintenance dans le secteur industriel. En équipant les machines et les équipements de capteurs connectés, les entreprises peuvent collecter et analyser en temps réel des données sur leur état de fonctionnement. Cette masse d'informations, traitée par des algorithmes d'apprentissage automatique, permet de prédire avec précision les pannes potentielles avant qu'elles ne se produisent.
La maintenance prédictive basée sur l'IIoT présente plusieurs avantages majeurs :
- Réduction des temps d'arrêt imprévus
- Optimisation des coûts de maintenance
- Prolongation de la durée de vie des équipements
- Amélioration de la sécurité des opérateurs
Cependant, la mise en place d'un système de maintenance prédictive efficace nécessite un investissement initial important en capteurs, infrastructures de communication et plateformes d'analyse de données. Il est également crucial de former le personnel de maintenance à l'utilisation de ces nouveaux outils et à l'interprétation des données générées.
Cybersécurité des systèmes de contrôle industriels (ICS)
Avec la connectivité croissante des systèmes industriels, la cybersécurité est devenue un enjeu majeur pour les entreprises du secteur. Les systèmes de contrôle industriels (ICS), autrefois isolés, sont désormais de plus en plus connectés à Internet et aux réseaux d'entreprise, les rendant vulnérables aux cyberattaques. Une brèche dans la sécurité d'un ICS peut avoir des conséquences catastrophiques, allant de l'arrêt de la production à des dommages physiques aux installations.
Pour faire face à ces menaces, les entreprises industrielles doivent adopter une approche holistique de la cybersécurité, intégrant à la fois des mesures techniques et organisationnelles. Cela inclut :
- La segmentation des réseaux pour isoler les systèmes critiques
- L'utilisation de protocoles de communication sécurisés
- La mise en place de contrôles d'accès stricts
- La formation régulière du personnel aux bonnes pratiques de sécurité
- La réalisation d'audits de sécurité et de tests de pénétration
La norme IEC 62443
, spécifique à la sécurité des systèmes d'automatisation et de contr
ôle de simulation en temps réel est essentiel pour anticiper et prévenir les cybermenaces potentielles.
Analyse big data pour l'optimisation des processus
L'analyse des big data est devenue un pilier de l'optimisation des processus industriels. Les entreprises collectent des quantités massives de données provenant de diverses sources : capteurs IoT, systèmes de production, chaînes d'approvisionnement, et retours clients. L'exploitation intelligente de ces données offre des opportunités sans précédent pour améliorer l'efficacité opérationnelle et la prise de décision.
Les techniques d'analyse avancées, telles que le machine learning et l'analyse prédictive, permettent aux industriels de :
- Identifier les goulots d'étranglement dans les processus de production
- Optimiser la consommation d'énergie et de ressources
- Prédire la demande des clients avec une plus grande précision
- Améliorer la qualité des produits en détectant les anomalies précoces
Cependant, la mise en place d'une stratégie big data efficace nécessite des investissements significatifs en infrastructure IT et en compétences analytiques. Les entreprises doivent également relever le défi de l'intégration des données provenant de systèmes hétérogènes et de la gestion de la qualité des données pour garantir la pertinence des analyses.
L'analyse big data n'est pas une fin en soi, mais un moyen puissant d'obtenir des insights actionnables pour améliorer continuellement les opérations industrielles.
Enjeux environnementaux et durabilité industrielle
Face à l'urgence climatique et aux pressions réglementaires croissantes, les entreprises industrielles sont contraintes de repenser leurs modèles de production pour les rendre plus durables. La transition vers une industrie plus verte n'est pas seulement une obligation, mais aussi une opportunité de créer de la valeur et de se différencier sur des marchés de plus en plus sensibles aux enjeux environnementaux.
Les principaux axes de transformation pour une industrie plus durable incluent :
- L'efficacité énergétique et l'utilisation d'énergies renouvelables
- L'optimisation de l'utilisation des ressources et la réduction des déchets
- L'éco-conception des produits pour faciliter leur recyclage et leur réutilisation
- La mise en place de chaînes d'approvisionnement responsables
L'économie circulaire émerge comme un paradigme prometteur pour concilier croissance économique et préservation de l'environnement. Elle implique de repenser les processus industriels pour minimiser les déchets et maximiser la réutilisation des matériaux. Des entreprises pionnières mettent en place des systèmes de remanufacturing, où les produits en fin de vie sont récupérés, démontés et reconditionnés pour créer de nouveaux produits, réduisant ainsi considérablement l'empreinte environnementale.
L'innovation joue un rôle crucial dans la transition vers une industrie plus durable. Des technologies telles que la capture et le stockage du carbone, les nouveaux procédés de fabrication à faible impact, ou encore les matériaux biosourcés, offrent des perspectives prometteuses pour réduire l'empreinte environnementale du secteur industriel.
Gestion des ressources humaines et formation dans l'industrie moderne
La transformation digitale et l'évolution rapide des technologies dans l'industrie ont un impact profond sur les compétences requises et la gestion des ressources humaines. Les entreprises industrielles font face à un double défi : attirer et retenir des talents dans un marché du travail compétitif, tout en assurant la montée en compétences de leur personnel existant.
La formation continue devient un enjeu stratégique pour les industriels. Les programmes de upskilling et de reskilling visent à adapter les compétences des employés aux nouvelles technologies et méthodes de travail. Ces initiatives peuvent inclure :
- Des formations sur les technologies de l'industrie 4.0 (IoT, IA, robotique)
- Le développement de compétences en analyse de données
- L'apprentissage de nouvelles méthodes de gestion de projet agiles
- La sensibilisation aux enjeux de cybersécurité
Les entreprises innovantes mettent en place des environnements de travail plus flexibles et collaboratifs pour attirer les jeunes talents. L'utilisation de technologies immersives comme la réalité virtuelle et augmentée pour la formation et la maintenance ouvre de nouvelles perspectives pour améliorer l'efficacité et la sécurité des opérations.
La gestion du changement devient une compétence clé pour les managers industriels. Ils doivent non seulement maîtriser les aspects techniques de la transformation digitale, mais aussi accompagner leurs équipes dans cette transition, en favorisant une culture d'apprentissage continu et d'adaptation.
Dans l'industrie du futur, la capacité d'une entreprise à développer et à mobiliser les compétences de ses collaborateurs sera aussi cruciale que sa maîtrise technologique.
En conclusion, les entreprises industrielles font face à des défis multiples et interconnectés : transformation digitale, optimisation des processus, innovation continue, durabilité environnementale et gestion des talents. Celles qui réussiront à naviguer ces changements en intégrant harmonieusement les nouvelles technologies, les considérations environnementales et le développement humain seront les mieux positionnées pour prospérer dans l'industrie du futur.